Achieving Welding Quality: Revealing the Secrets of WPS Implementation and Optimization
In the realm of welding, attaining quality is a pursuit that hinges on the careful application and optimization of Welding Treatment Specs (WPS) By diving into the crucial components, strategies, obstacles, and best techniques connected with WPS, a world of welding quality waits for those who are eager to explore its midsts.
Significance of WPS in Welding
The Significance of Welding Procedure Specifications (WPS) in the welding market can not be overstated, functioning as the foundation for ensuring uniformity, quality, and safety in welding procedures. A WPS provides detailed instructions on how welding is to be performed, consisting of necessary variables such as products, welding processes, joint style, filler steels, interpass and preheat temperature levels, welding currents, voltages, travel rates, and much more. By sticking to a well-defined WPS, welders can preserve harmony in their work, causing regular weld high quality across various tasks.
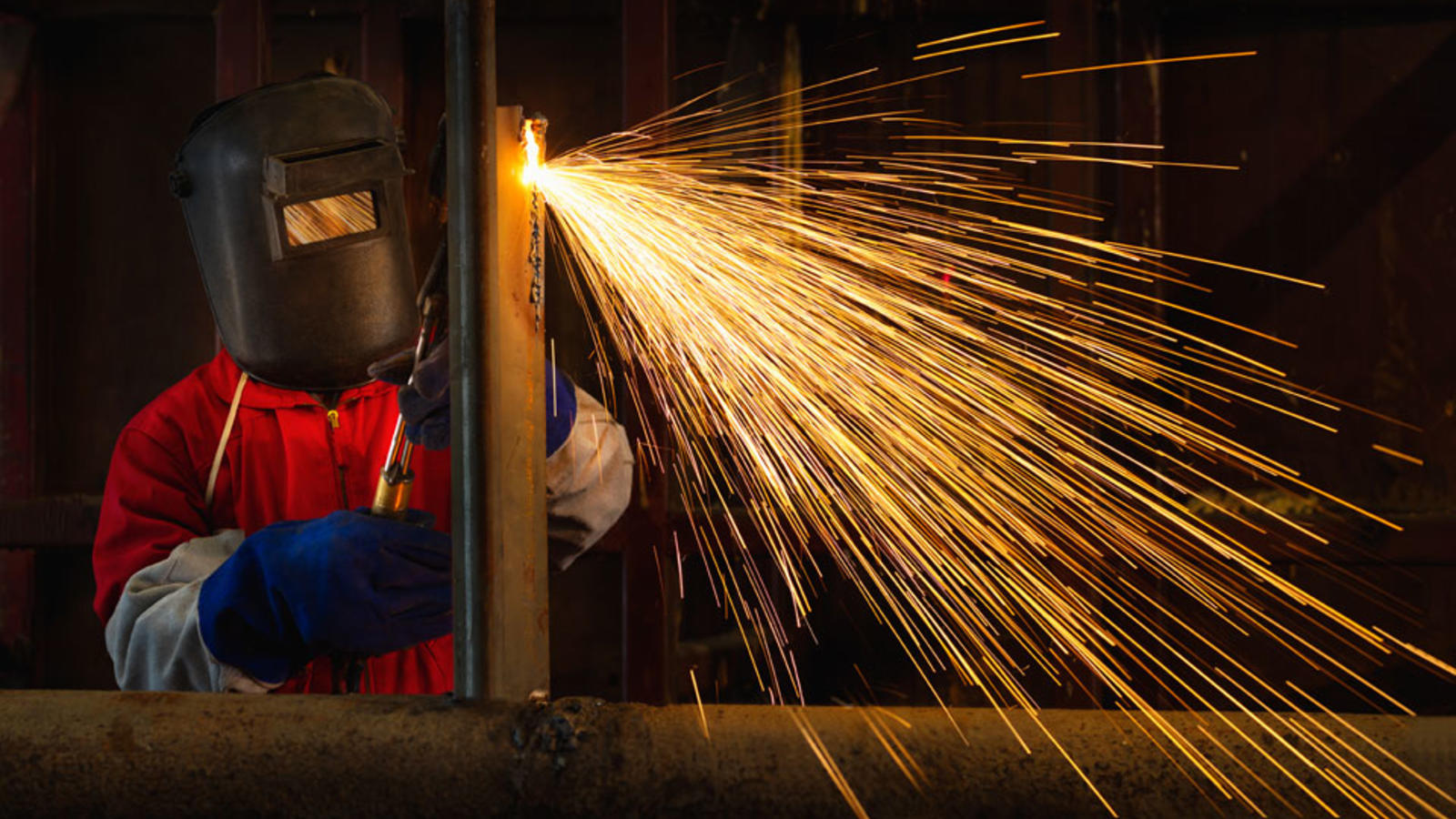
Crucial Element of WPS
Talking about the indispensable components of a welding procedure requirements (WPS) is essential for comprehending its duty in welding procedures. One essential element of a WPS is the welding procedure specification, which describes the certain welding procedures to be made use of, such as gas tungsten arc welding (GTAW) or protected steel arc welding (SMAW) By including these vital components into the WPS, welding treatments can be standard, making certain high quality, effectiveness, and safety and security in welding operations.
Strategies for WPS Optimization
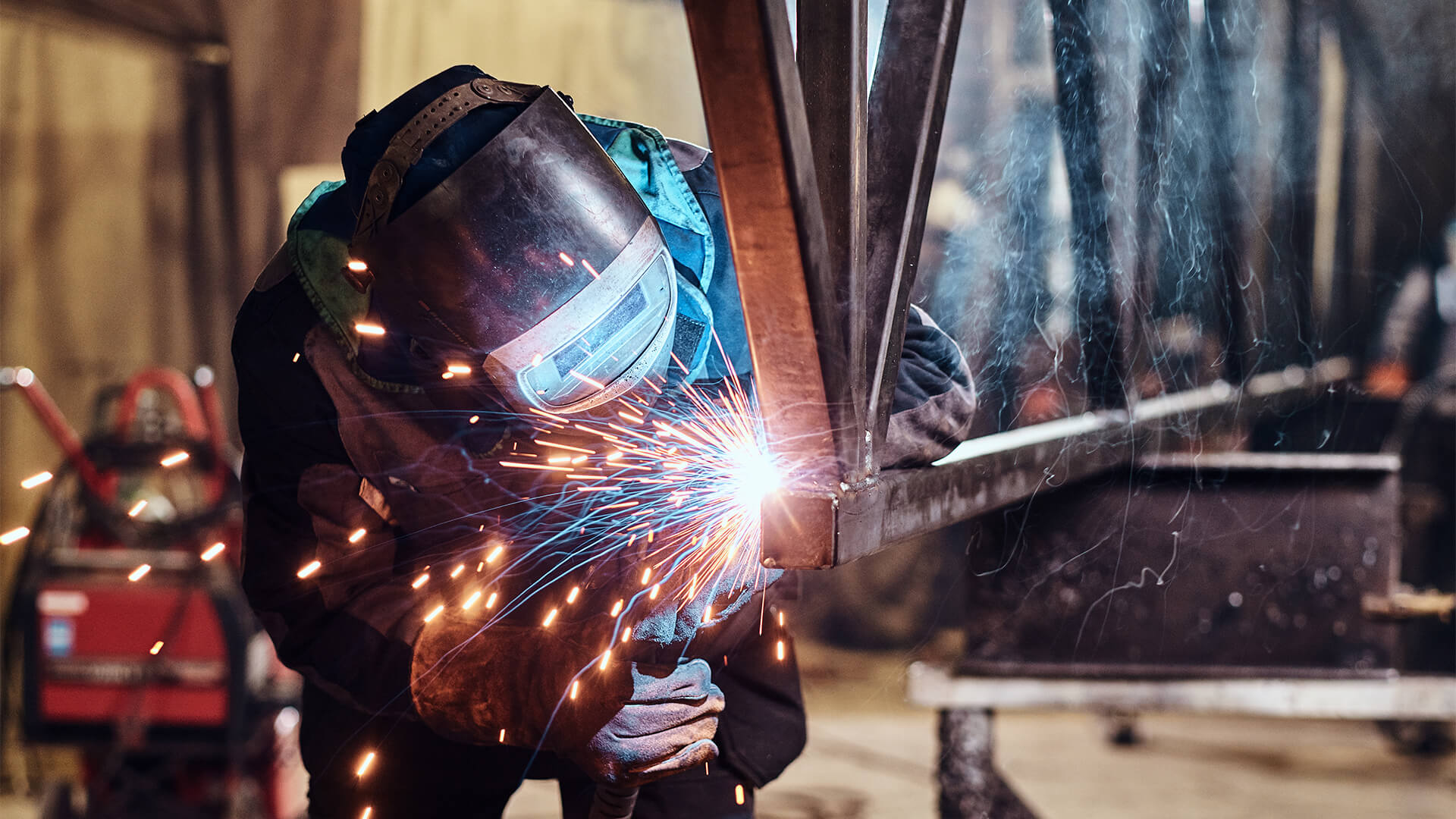
Second of all, training and credentials of welding workers according to the certain needs of the WPS is extremely important. Supplying comprehensive training programs and guaranteeing that welders are accredited to perform treatments outlined in the WPS can bring about better welds and decreased rework.
Additionally, leveraging technology such as welding software program and tracking systems can assist in maximizing WPS. These devices can assist in tracking variables, making sure specifications are within defined limitations, and giving real-time responses to welders, allowing them to make instant adjustments for enhanced weld quality.
Usual Obstacles and Solutions
Dealing with challenges in executing the strategies for WPS optimization can prevent welding operations' effectiveness and top quality. One usual obstacle is insufficient training or understanding of the welding pop over to these guys procedure specs (WPS) among the welding team.
An additional difficulty is the lack of correct paperwork and record-keeping, which is crucial for WPS optimization. Without clear documents of welding specifications, products utilized, and inspection outcomes, it comes to be challenging to determine areas for renovation and guarantee uniformity in welding procedures. Implementing a durable documentation system, such as electronic welding administration software application, can help enhance record-keeping and help with data evaluation for constant improvement.
In addition, inconsistent welding equipment calibration and maintenance can posture a significant obstacle to WPS optimization. Regular equipment checks, calibration, and upkeep schedules should be followed purely to guarantee that welding criteria are accurately regulated and preserved within the defined resistances (welding WPS). By dealing with these common obstacles with aggressive remedies, welding operations can improve efficiency, quality, and total welding quality
Best Practices for WPS Execution
To guarantee successful WPS welding WPS application in welding operations, adherence to industry requirements and thorough focus to information are paramount. When starting WPS application, it is crucial to begin by completely comprehending the particular welding needs of the job. This entails a detailed testimonial of the welding procedure specs, materials to be bonded, and the environmental problems in which the welding will happen.
When the demands are clear, the following step is to choose the suitable welding procedure that straightens with these specs. This entails consulting the pertinent codes and standards, such as those supplied by the American Welding Society (AWS) or the International Organization for Standardization (ISO), to make certain conformity and quality.
In addition, recording the entire WPS implementation process is vital for traceability and top quality control. Detailed records should be maintained regarding welding parameters, material preparation, preheat and interpass temperatures, welding consumables used, and any kind of inconsistencies from the initial treatment. Routine audits and reviews of the WPS can help identify locations for renovation and make her explanation sure continuous optimization of the welding process.
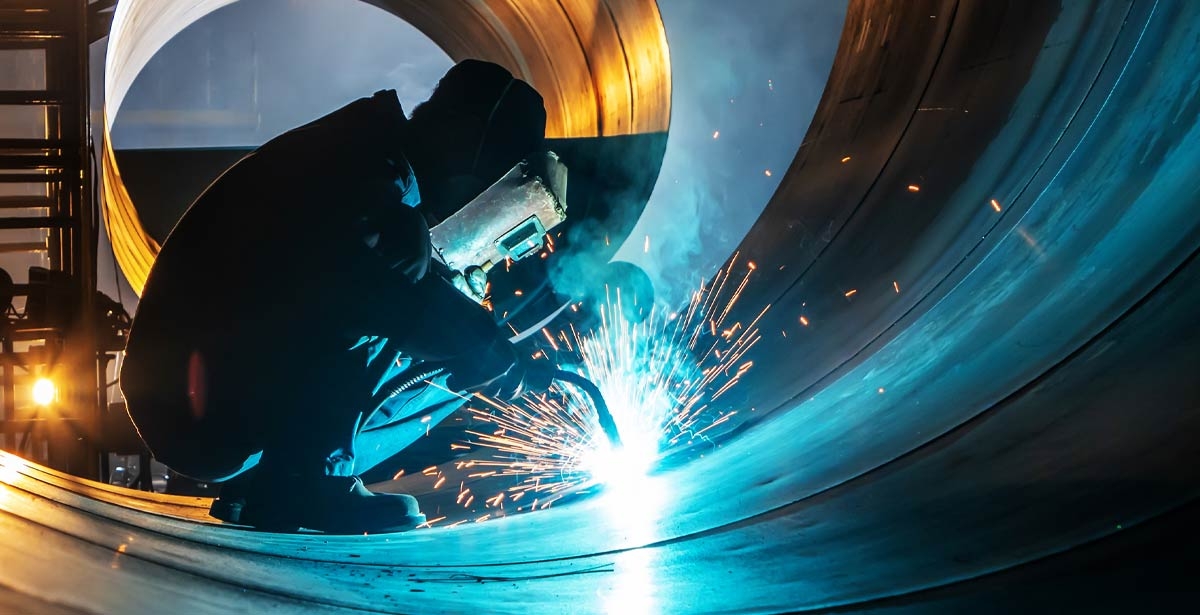

Conclusion
Finally, the execution and optimization of Welding Procedure Specs (WPS) is crucial for accomplishing welding quality. By understanding the crucial elements of WPS, applying efficient approaches for optimization, addressing typical difficulties, and adhering to best practices, welders can make sure high-grade welds and safe working conditions. It is critical for professionals in the welding industry to prioritize the appropriate implementation of WPS to improve total welding performance and accomplish wanted outcomes.
The Value of Welding Treatment Specifications (WPS) in the welding market can not be overemphasized, serving as the backbone for making certain uniformity, top quality, and safety in welding procedures. A WPS gives detailed guidelines on just how welding is to be lugged out, consisting of crucial variables such as products, welding procedures, joint style, filler steels, interpass and preheat temperature levels, welding currents, voltages, travel speeds, and a lot more. One vital element of a WPS is the welding process spec, which describes the specific welding processes to be used, such as gas tungsten arc welding (GTAW) or secured steel arc welding (SMAW) By integrating these vital aspects into the WPS, welding procedures can be standardized, guaranteeing high quality, effectiveness, and security in welding procedures.
It is imperative for professionals in the welding industry to prioritize the proper implementation of WPS to enhance overall welding performance and achieve desired outcomes.